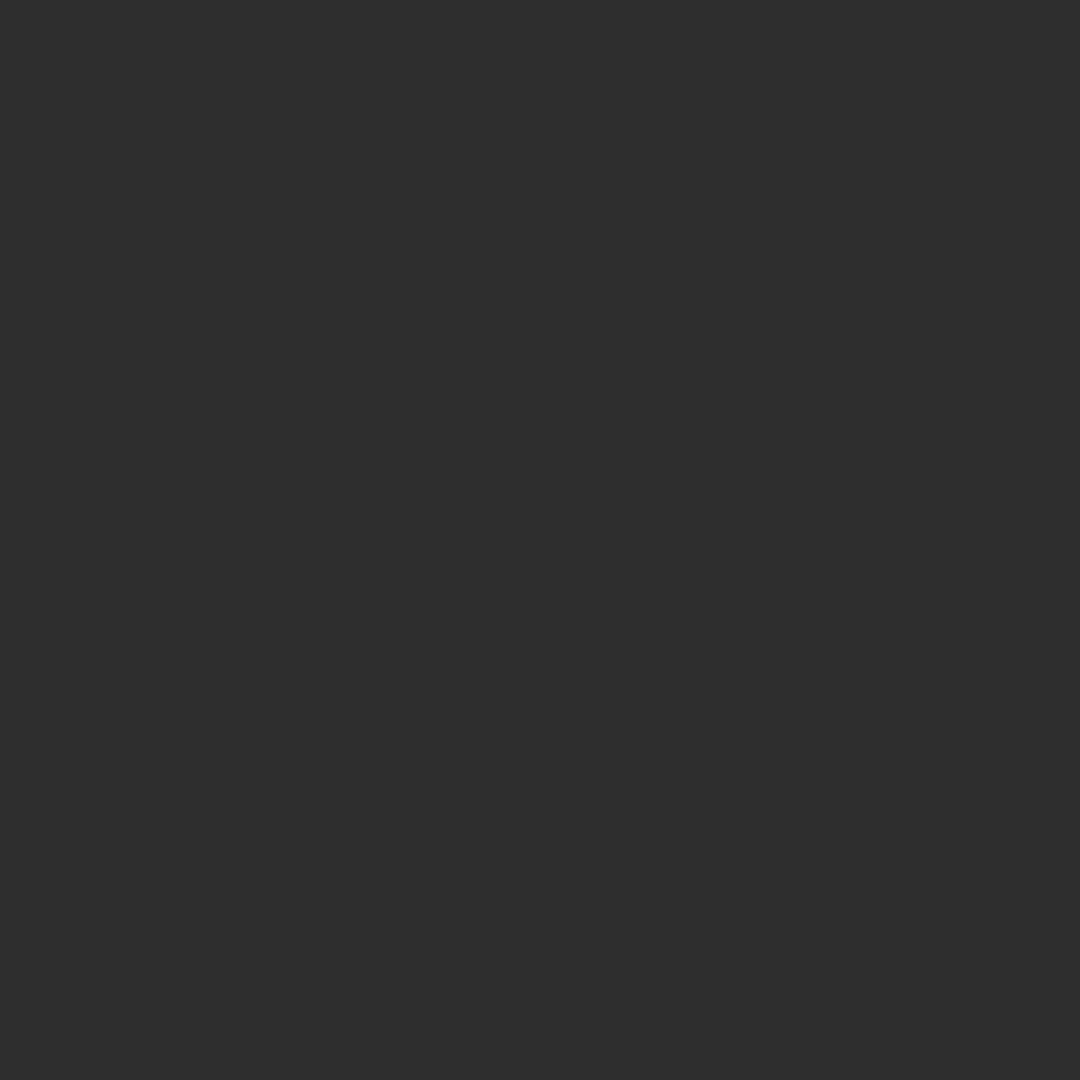
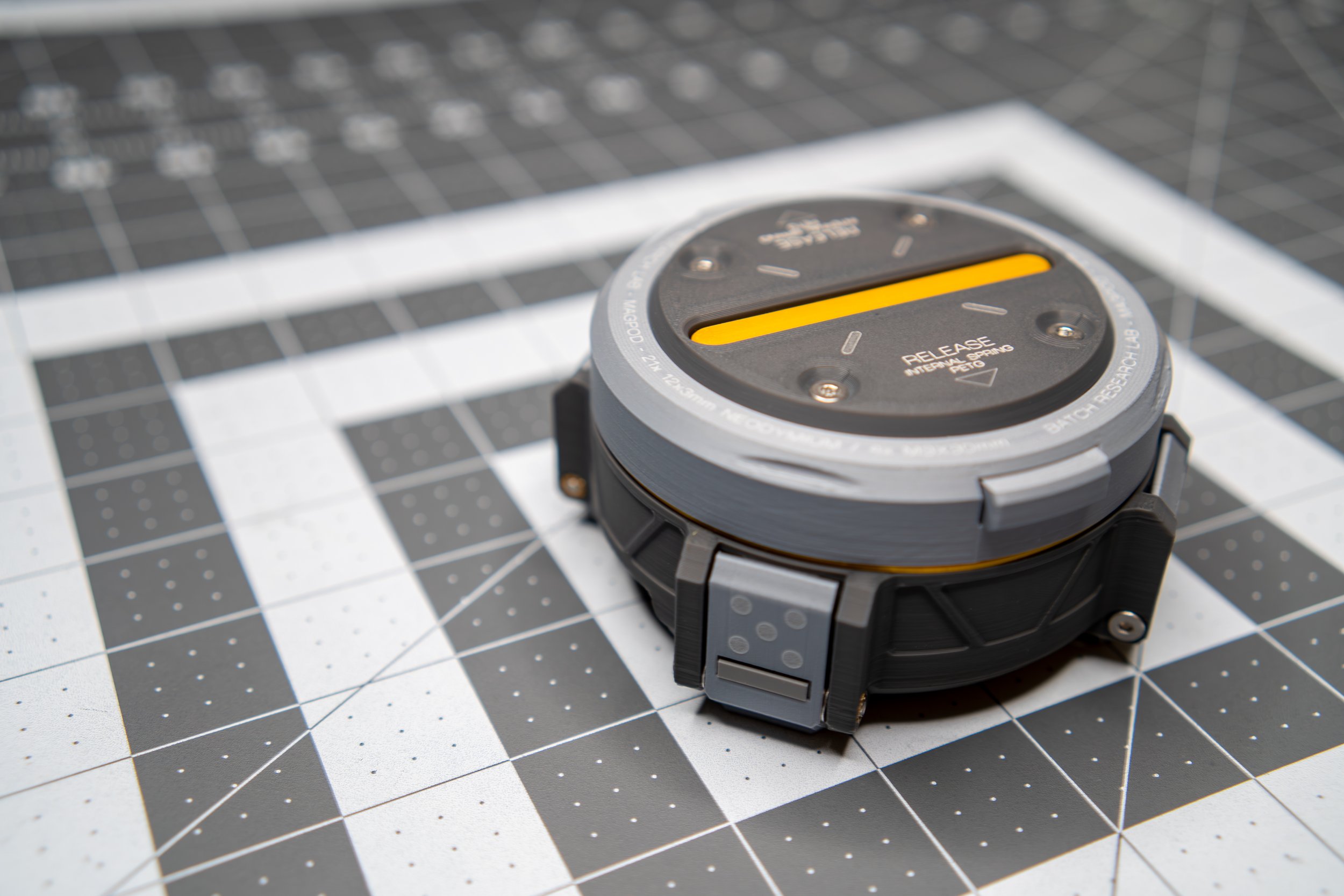
PROJECT
Magnet Pod Build
This is an overview of the build process for our Magnet Pod design. This is the culmination (or at least, current state) of dozens of iterations and testing. We tried different numbers of, different placement configurations, different shapes, and different thicknesses of magnets. Many magnets gave their lives to help us reach this point, forever entombed in the sealed crypts of filament that litter the unforgiving path of progress.
If you want to try printing and building one of these yourself, we’ve made the files available in our store.
Reference files can be found in the Materials Reference accordion at the bottom of the page
A lot of magnets
Though for this build, there are some points about slicer and print setup we wanted to make sure to convey. There are a lot of magnets that need to be embedded (21, to be exact), and we did our best to make optimal decisions about which way to orient each part to the plate.
The main body requires the print to be paused in two places; once for the magnets embedded in the bottom, and once for the magnets in the sides.
This design uses thirteen 12x3 mm disc magnets in the floor of the main body. We were trying to incorporate enough magnet strength to prevent the pod from sliding down a vertical surface, while also maximizing interior space.
Which is why the magnet configuration is flatter and wider. Initially, the floor used thinner 12x2 mm magnets, but we found that the pod still slid down on some surfaces, even when empty.
The magnets in the main body floor were placed in a checkerboard pattern, with all the outer and center magnets having their north pole facing down.
The main body uses an additional four 12x3 mm disc magnets in four angled slots. These retain the feet in the vertical, tucked position when the pod is not attached to a metallic surface.
These magnets were placed so that north faced inward toward the main interior cavity.
Depending on the material, used the print, there may be issues with these magnets being repelled by the magnets in the floor. If you encounter any issues with this, using a small dab of cyanoacrylate glue on the insertion end, then holding it down in its magnet cavity should get it to stay in there and prevent it from popping up. At least long enough for them to get sealed securely inside.
We printed the feet sideways to help ensure that the screw shafts stayed round. But because of this, the magnet cavities needed to be modeled as a square to minimize any potential issues when dropping the magnets in.
These are also the same size as the other magnets in the project; 12mm in diameter and 3mm thick. At least that's what they're listed as. In reality, and as usual, they're actually a bit smaller. The magnets in the feet were oriented so that north faced up toward the thicker part of the print.
Even though these were round magnets going into square holes, the printer didn’t seem to have any issues bridging the gap and sealing them in. Early-on, we did have some issues with bed adhesion when printing the feet, so we used glue and a brim. But we set the brim-object gap pretty wide at 0.23mm and the parts came off without the need for any major clean-up.
There is also a version of the foot that is designed to accommodate the addition of a rubber or silicone pad. The recess is 15 x 4 x 0.5 mm, and is designed to work with 1 mm thick material that should protrude just enough. We used self adhesive silicone and it worked pretty well.
The additional points of grip help prevent the pod from sliding down when it’s attached to slick vertical surfaces.
Magnet orientation guide
The lid buttons were printed upside down, with the largest face on the build plate. We tried both normal and tree supports, and the normal supports detached much cleaner from the latch lip.
The lid ring was printed upside down as well, and tree supports were manually painted on to the overhang surfaces for the button holes. After printing, those button holes should be cleaned up pretty well to ensure that buttons slide in and out freely.
We used a plastic tool when scraping the surface to avoid marring or scratching the part.
The internal spring for the buttons needs to be printed using a material that is resilient and flexible. Something that is stiff and brittle will not work, such as a matte PLA. We tried PETG and it has worked well so far.
The revised magnetic top cap is printed upside down with the magnets placed in with the north side up when the print is paused at the appropriate time.
This will help center the top cap to the underside of another MagPod stacked on top.
Also included in the file set is a simple gasket, which we recommend to be printed in something flexible like TPU. It fits around the flange, and between the lid and the main body.
It functions as a washer that aids when spinning the lid till the buttons seat into the notches.
(if you don’t want to use the gasket, there are also slightly taller versions of the lid included in the file set)
Installing the M3 inserts into the center riser plate should be fairly uncomplicated, and cold-pressing the final millimeter helps to ensure a clean, flush installation.
Assembly of the lid should be relatively straightforward, but it did help to place the lid ring upside down on a work surface for installation of the buttons and the spring. Once the spring is in place, it should hold the buttons in for the next step.
Hat-tip to Slant 3D for teaching everyone about printed springs in their video ;)
The center riser plate retains both the internal spring and the buttons; and using four 6mm countersunk M3 screws, the top plate sandwiches them securely in between.
The buttons should slide freely in and out of the lid ring, automatically pushing back outward upon release.
When pressing the M3 inserts into the bottom slot walls of the main body, we used only enough pressure to ensure that each insert sank in.
This part of the print is relatively thin and unsupported, so there is a risk of warping the hinge wall downward with too much pressure.
We also cold pressed along the cool edge of that wall to help ensure that we pressed parallel to the wall and not at an angle.
It’s best to wait a little while to ensure that the plastic has fully re-solidified before installing the feet.
Once the main body has fully cooled, the 30mm countersunk M3 screws can begin to be threaded in.
At first, screw them in just until there is about a half millimeter protruding on the other side of the wall. This will allow the placement of a metal M3 washer so that it doesn’t slide off.
Then one of the feet can be inserted into the slot and the screw can be threaded-in further through the channel in the foot. You will know if you have properly installed all the magnets if the foot magnetically stays in place during the screw installation.
Before threading the screw all the way through, insert a second metal M3 washer in between the foot and the main body wall. These two washers on either side of the foot prevent contact and binding of the foot against the slot wall.
Note that we used the metal M3 washers instead of the plastic type for this because the metal washers were available in thinner thicknesses.
Adjust the tightness of the screw to make sure the foot is secure, but still rotates freely. Then repeat the process for the other 3 sides.
Completed Magnet Pod Units (updated version)
Interior Dimensions
The opening is 86 mm in diameter, and the cavity is about 30 mm deep.
Interior Volume
Interior volume is about 165 cubic cm.
Weight Capacity
Vertical holding power holds at about 17 oz., or 500 g (*when equipped with the silicone foot pads).
On brushed stainless steel
Underside
Accessory attachment port
Accessory upgrades
Hex bit insert
Lid notches for stacking
Zeon Chain Mine alternate version
-
If you are interested in what we used for this process, you can find our materials below.
Hardware:
Bambu X1 Carbon
WhamBam 258 x 258 Flexi Plate with Pre-Installed PEX Build Surface
xTool F1
Heat-set insert press with tips for M3 inserts
Software:
Shapr3D Version 5.710.0 (7459)
Bambu Studio 1.9.7.52xTool Creative Space v2.2.21
Materials:
4x M3 countersunk flat head screws 30 mm (hex socket preferred)
4x M3 countersunk flat head screws 6 mm (hex socket preferred)
16x M3 heat-set insert 4mm deep
8x M3 stainless steel flat washers 6 mm OD, 3 mm ID, 0.5 mm thickness
21x 12x3mm Rare Earth Magnets (round disc)
Materials (optional):
1x M3 countersunk flat head screws 14 mm (hex socket preferred)
4x M3 buttonhead head screws 8 mm
1x M3 heat-set insert 4mm deep
1x Wireless LED light with tap and remote control
1x Submersible wireless LED light with remote control2x Triangle rings
-
-
*Please remember that using lasers on synthetic materials always runs the risk of putting harmful chemicals into the air. So, before beginning, don't forget to ensure that you have proper ventilation and to use hoods and air filtration whenever possible.